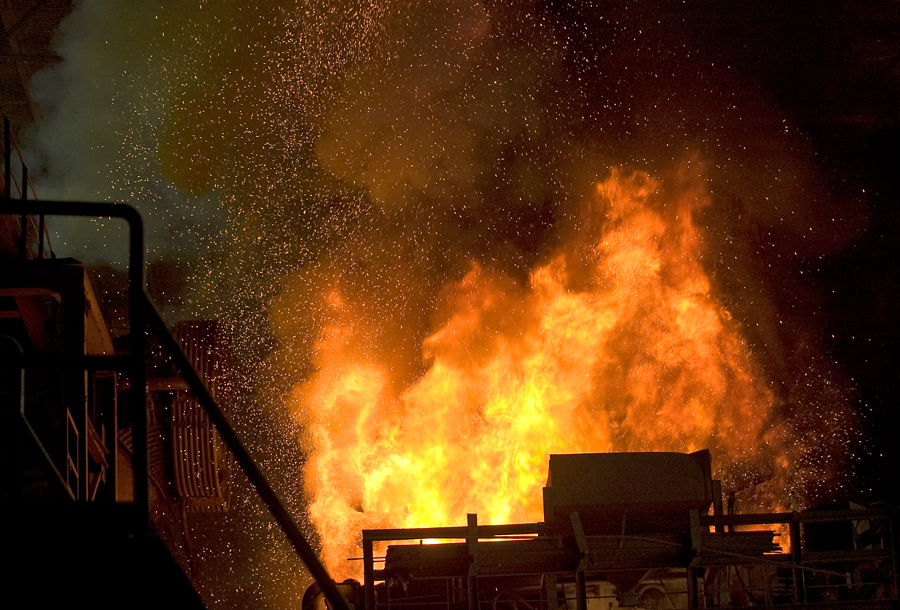
Steel was first made thousands of years ago. The discovery that heating up iron ore in a hot enough charcoal fire could purify the iron into a strong and valuable material was the start of the Iron Age. In many ways, things have changed very little since then.
Global iron and steel production accounts for 7% of society’s carbon emissions. Making steel generally involves burning coal in a blast furnace to produce the very high temperatures required to turn iron into steel. The coal is used both as a feedstock and as a fuel. Steel is made from iron and a substance called coke, which is basically coal that has been carbonized at high temperatures. Coal itself is burned to provide the high temperatures needed.
A new analysis from the Global Energy Monitor think tank shows that the global steel industry is slowly embracing electric-arc furnaces to produce the necessary heat, which is a cleaner alternative. The analysis found that 43% of forthcoming steelmaking capacity will rely on electric-arc furnaces, up from 33% last year.
According to the study, the shift to cleaner steel is not happening fast enough. To meet the emissions reductions goals of the Paris Climate Agreement, electric-arc furnaces must account for 53% of global steelmaking capacity by 2050. Based on the current plans, those furnaces would only account for 32% of total capacity by that year.
In order to meet these goals, the steel industry will need to retire or cancel about 381 million tons of coal-based manufacturing capacity and add 670 million tons of electric-arc furnace capacity.
**********
Web Links
Steel Industry Pivoting to Electric Furnaces, Analysis Shows
Photo, posted March 3, 2012, courtesy of Jeronimo Nisa via Flickr.
Earth Wise is a production of WAMC Northeast Public Radio
Digging a little deeper into the sources a lot of the concerns about this report were probably cut for content.
https://e360.yale.edu/features/can-the-worlds-most-polluting-heavy-industries-decarbonize
This dives into why carbon is used in the blast furnace operation / to reduce the ore and make pig iron as well as being a heat source. This reduction is what combines the oxide from the ore and the carbon from the coke to make CO.
This article also outlines the availability of scrap being about 85% already collected and used in recycling limiting the amount of raw material available for the more environmentally friendly EAF process of steel. So there isn’t enough scrap steel to sustain the likely future needs of only using the EAF process.
Also of consideration is the quality of steel that can be made from the integrated process is more diverse and cleaner than can be made in the EAF / Ladel process. Some steel end uses have these requirements and cannot be sourced through the EAF routing.
I do agree exploring ways to reduce ore to iron using less carbon technology is the way that we should be going, but that is still MANY years out before commercially viable.
In most articles it is implied we can just replace the blast furnace / BOP steelmaking process with EAF steelmaking process and we’ll all be living in a greener world, but the reality is much more complicated and the technologies are not interchangeable on the whole.