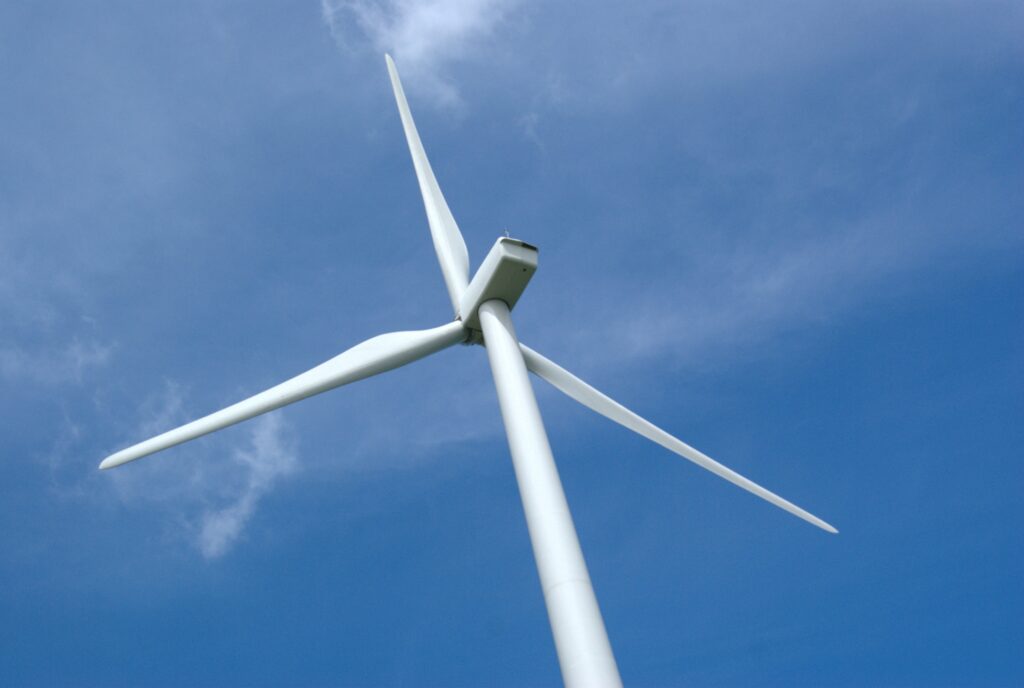
The blades of modern wind turbines can be longer than the wing of a Boeing 747. Their useful lifetime is perhaps 20 years and after that, they can’t just be hauled away. They end up being cut up with special industrial saws to create pieces small enough to be strapped to a tractor-trailer. Then, they end up in landfills. There are thousands of blades being removed each year and those numbers are growing.
Wind turbine blades are currently manufactured using thermoset resin, which cannot be recycled. It is also energy-intensive and manpower-intensive to produce.
Researchers at the National Renewable Energy Laboratory in partnership with Arkema Inc of Pennsylvania have demonstrated the feasibility of using thermoplastic resin instead to make wind turbine blades. That material can be recycled and can also enable longer, lighter-weight, and lower-cost blades. Using thermoplastic could also allow manufacturers to build blades on site, alleviating the problems of transporting ever larger turbine blades.
Current blades are made primarily of composite materials like fiberglass infused with thermoset resin. The manufacturing process requires additional heat to cure the resin, which adds cost and time. Thermoplastic resin cures at room temperature and requires less labor. With regard to recycling, thermoplastic resin, when heated above a certain temperature, melts into its original liquid resin and can be reused.
NREL has demonstrated the feasibility of the thermoplastic resin system by manufacturing nearly identical blades using both the standard materials and the thermoplastics. NREL has also developed a technoeconomic model to evaluate the cost benefits of using thermoplastic resin.
**********
Web Links
News Release: NREL Advanced Manufacturing Research Moves Wind Turbine Blades Toward Recyclability
Photo, posted June 28, 2008, courtesy of Patrick Finnegan via Flickr.
Earth Wise is a production of WAMC Northeast Public Radio.
Leave a Reply